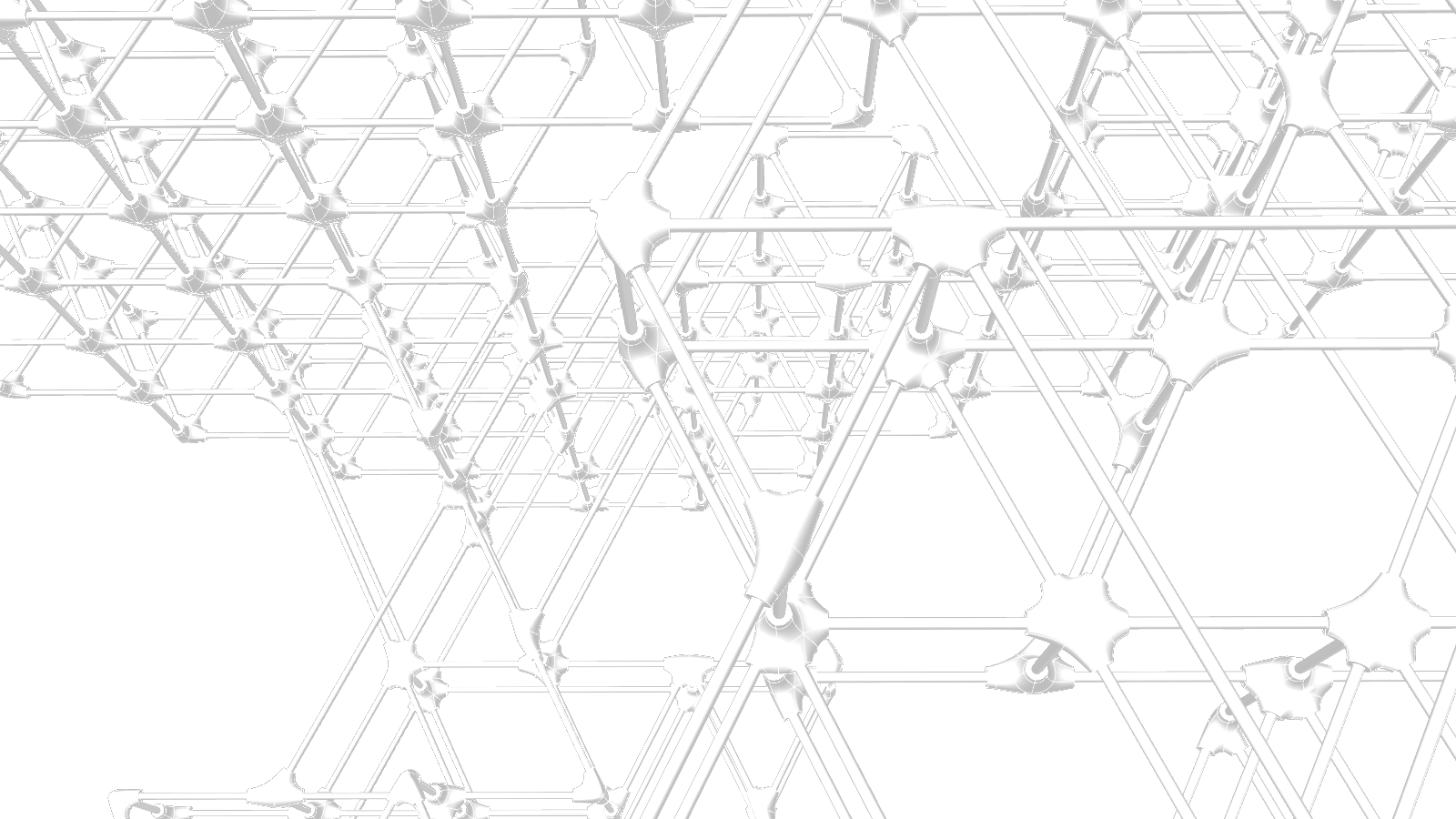
Smart_Materials
Data Driven Design and Material Architecture
Venice Architecture Biennale | 2023
OVERVIEW | OBJECTIVES
Smart_Materials: To design and explore the computational underpinnings of FabriCity_XR from LINE (Lattice) to VOLUME (Additive Manufacturing)
In collaboration with the Design, Computation, and Fabrication studio, the Smart Materials elective was established to create the scripts behind the design and excel related research in a pseudo designer-to-client fashion. In 2022 the class worked to design the honey-combing logic, the node generation, the selection of rods, and the concrete 3D printing toolpaths needed for execution of the exhibition’s design. An AR workflow was developed for rapid construction at the venue to maximize the effectiveness of each team member.
LINE TO VOLUME | METHODS
Honeycombs
In mathematics, a honeycomb is a form that can be copied and reoriented to fill a given space without gaps. The idea was to develop upon the studio’s concept of porosity literally – the elective sought to subdivide these honeycombing ‘cells’ into smaller sub-cells. Only cubes, rectangular-prisms, and the tetrahedron-octahedron honeycombs have this property of self-similarity - even after the concept was dropped, the tetrahedron-octahedron honeycomb proved popular and remained until the completion of the project.
Node Generation
Determined by physical constraints, the elective was aware that four different radii of wooden rods were to be used as edges in the exhibition, but the precise position and radius of each rod was determined largely by the weight of the nodes themselves – therefore, the elective needed to design an adaptable system that could generate nodes for any possible configuration of elements. Once a preferred node-generating script was chosen, edge elements could be determined and the nodes finalized.
The working solution consisted of two equally-long partitioned lists, one containing all the edges for each node as sub-lists and the other containing the corresponding radii. These lists of lists were then used to generate the nodes, subtract the rod-geometry to allow the nodes to interface, and then deboss the appropriate tags. The rod-geometry included holes for adding tensioning pins as the design was unstable in tension, and the tags were chosen such that their IDs all faced the same direction whenever the exhibition was complete, allowing for quick orientation.
Lattice Optimization
Once the design was largely finalized, physics simulations were run to determine the most and least compressed elements, with a domain chosen to flatten the range into the four distinct radii; elements under more compression need a larger radius than those under negligible compression or tension. Likewise, elements were added or removed based on their relevance to the stability of the design. Once the lattice was finalized, using the average weight of the nodes printed from a prototypal model, these simulations were run and used to re-generate the nodes in the system.
Concrete Printing Toolpaths
To keep the design consistent, the pedestals were designed using the tetrahedron-octahedron honeycomb as well – however, the precision and slope of the original honeycomb was deemed too low to be viable, so a vertically scaled version was utilized instead. Several iterations of the pedestals were generated to best determine aesthetic quality and feasibility – four were selected, and disregarding the versions printing using the BigREP printer, the pedestals were printed by ExtreE without prior prototyping.
AR Workflow
Using the tags generated during node construction, AR tags were created and sorted based on layer and position within said layer. A simple filter/gate system was utilized to switch between seeing the entire exhibition, just the nodes, just the nodes of a given layer and specific nodes if desired, and to toggle the tags in the display. Toggling the display proved useful during construction, as it allowed for verbally describing nodes whenever a tag was less obvious to crewmembers without a Hololens. Additional support included color-coding rods based on length and radius, but this proved unnecessary for construction and thus a waste of the small computer’s resources.
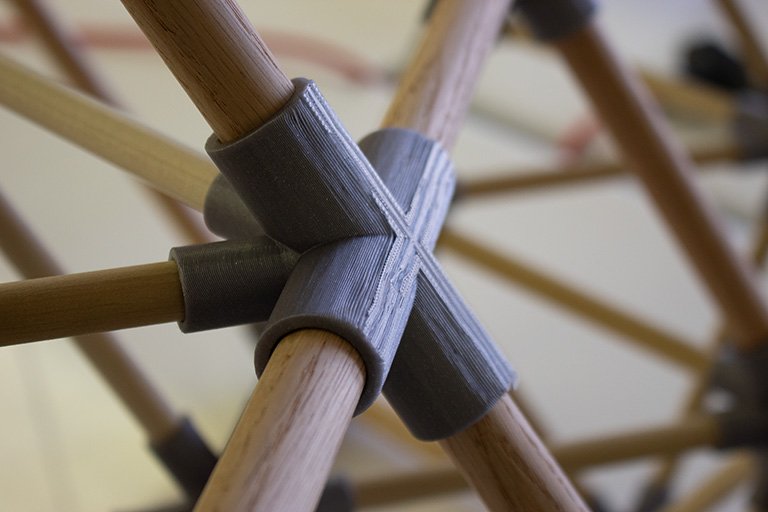
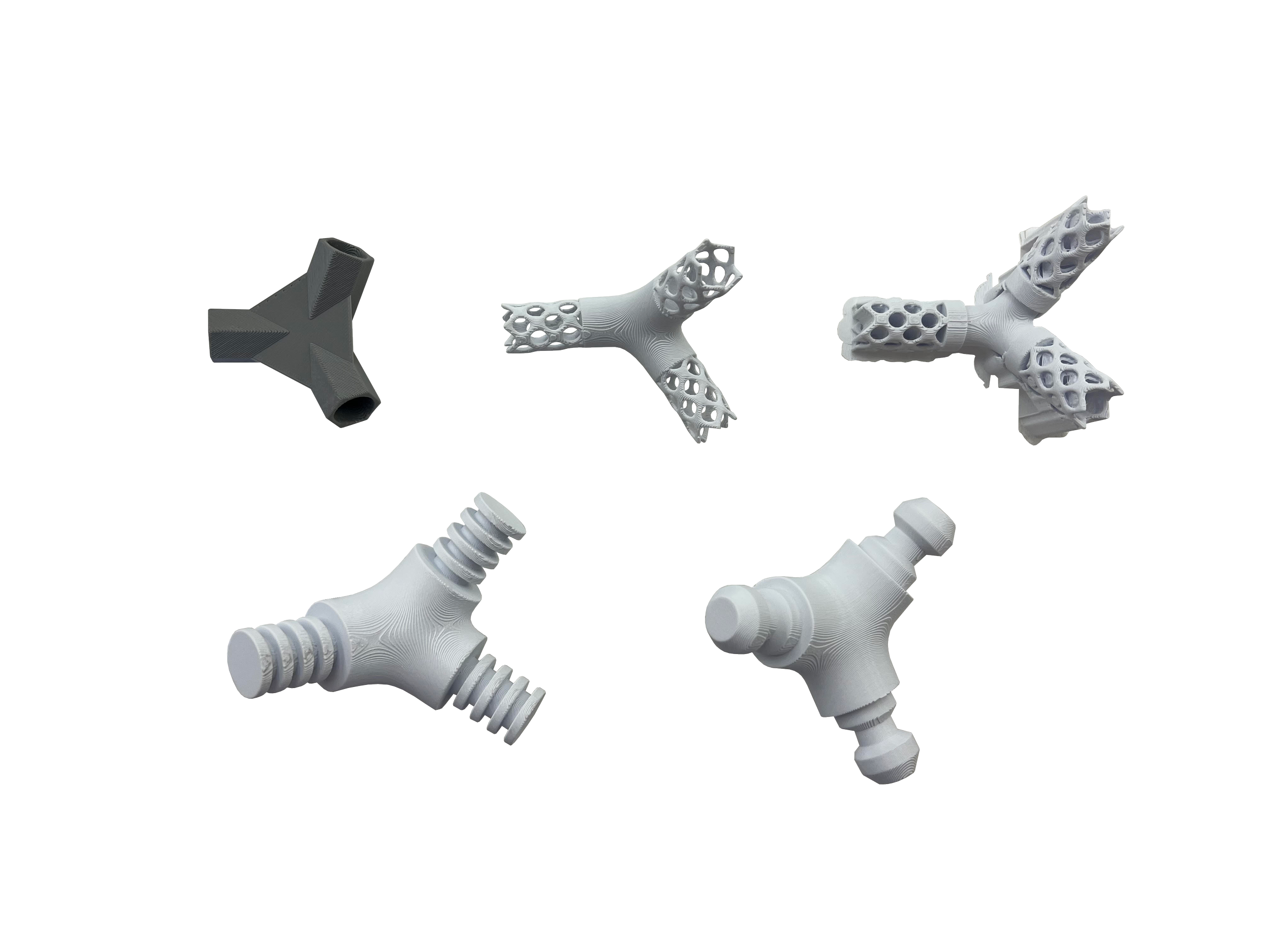

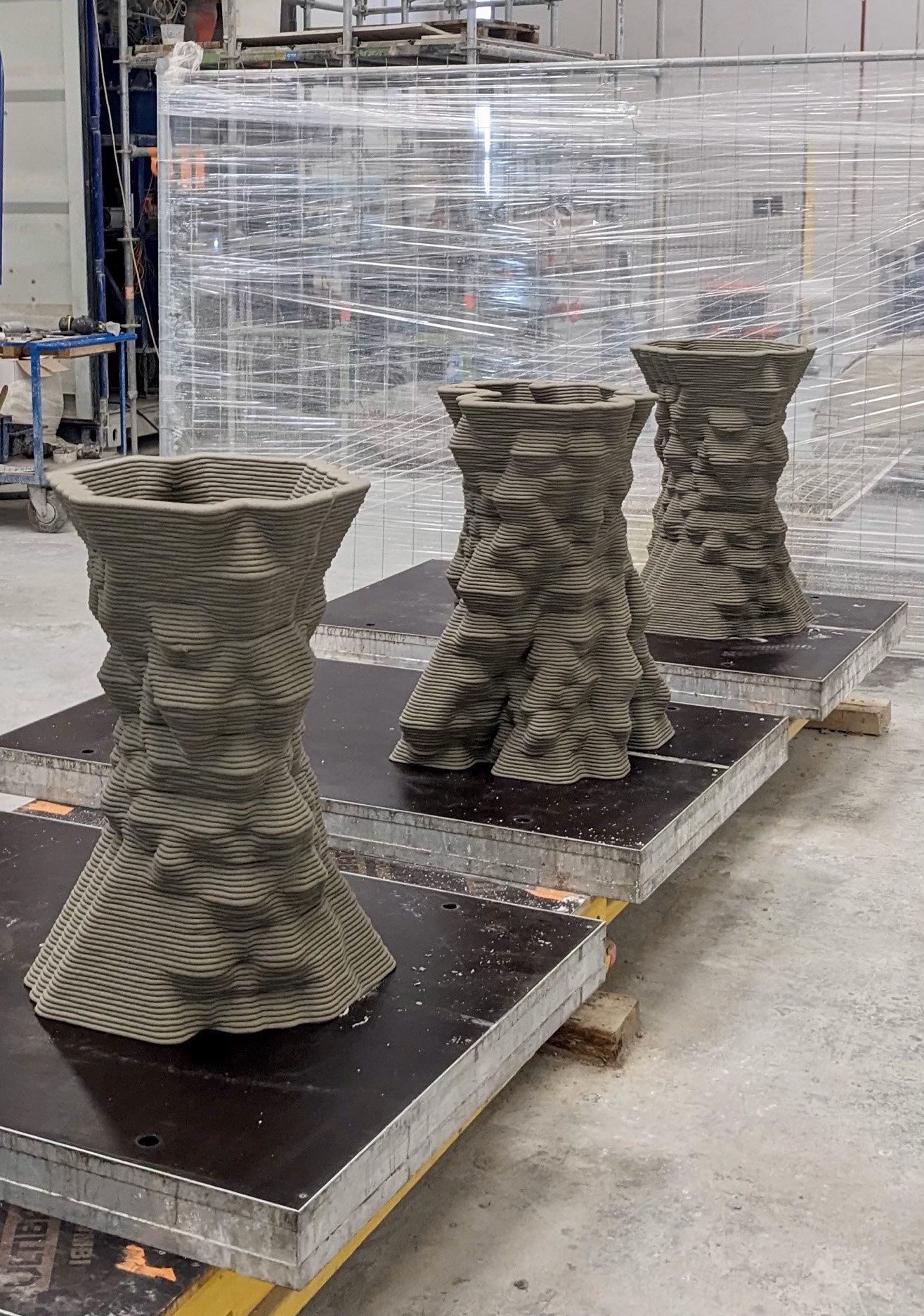
Texas Tech University Huckabee College of Architecture Core Team:
Principals: Assoc. Prof. Dr. Sina Mostafavi | Graduate Research Assistant: Sarvin Eshaghi | Teaching Assistant: Cole Howell | Participating Students: Abel Gonzalez, Cole Howell, Jiwon Chung, Luiz Trujillo, Saul Ortega
TTU HCoA Additional Support:
Fabrication support: TTU-HCoA Digital Fabrication, 3D Printing and Robotic Labs, Hinton Vick and Mike West