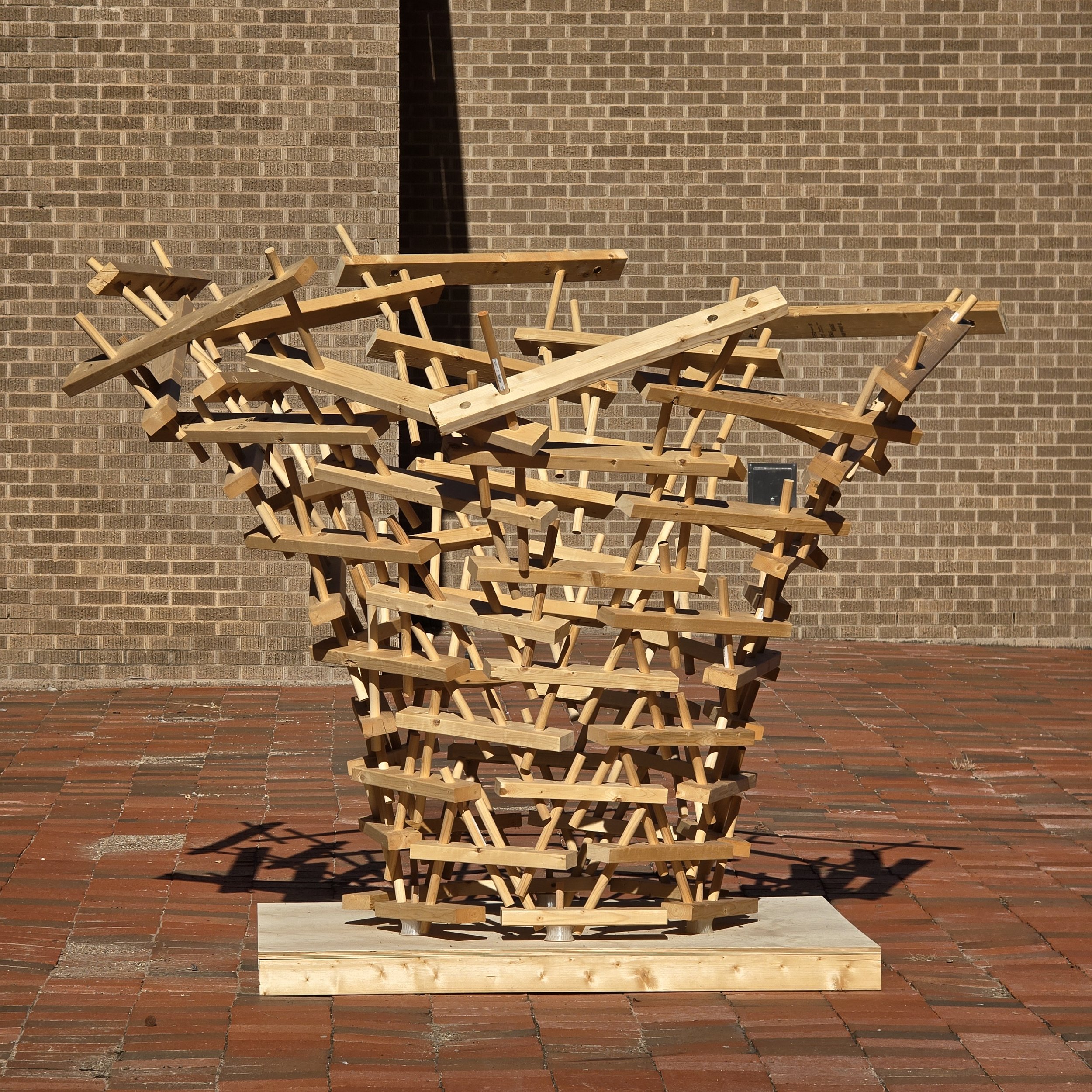
Urban Community Food Podium
Integrated Design to Robotic Production & AR-Enabled Assembly Systems
3 Projects: Landscape + Canopy, Oven + Canopy, Landscape + Oven
OVERVIEW | OBJECTIVES
The Urban Community Food Podium is a research-driven project that merges advanced digital design, robotic fabrication, and augmented reality (AR)-enabled construction to support food resilience and community empowerment. Developed in collaboration with the South Plains Food Bank, the podium serves as a modular, adaptive infrastructure for urban food production, distribution, and education. Situated within the context of Lubbock, Texas, this initiative addresses regional food insecurity by providing a replicable model that integrates local partnerships and technology-driven construction.
The design process incorporates parametric modeling and robotic production to optimize structural components for material efficiency and precision. These components are assembled using AR-enabled systems that guide users through step-by-step visual instructions, making construction accessible to a broader range of participants—including volunteers and community members—regardless of prior building experience.
Functioning as a flexible framework, the Food Podium accommodates raised garden beds, shaded gathering spaces, storage units, and educational displays. It supports the South Plains Food Bank’s mission by expanding their outreach through spatial infrastructure that is co-designed and co-built with the community. This project envisions a future where architectural production is localized, inclusive, and aligned with urgent social needs—redefining how we grow food, share knowledge, and build cities from the ground up.
INFO | CREDITS
Hi-DARS lab Core Team:
Principal: Associate Prof. Dr. Sina Mostafavi
Graduate Research Assistants: Bahar Bagheri, Edgar Montejano
Teaching Assistants: Brodey Myers
Projects:
1_ Landscape + Canopy:
Brandon Paleo, Garrett Whitehead, Gunner Murrell, Jack Dittrich, Jacklyn Hurtado, Jakelin Silva, Kathleen Gutierrez, Max Halwas
2_ Oven + Canopy:
Aaron Malavolta, Amanda Gomez, Apollo Nyoma, Caleb Scott, Gabe Herrera, Harmony Smith, Mattia Hajmeli, Robin Mutchler
3_ Landscape + Oven:
Bahar Bagheri, Bernardo Lopez, Colin Ayers, Corinne Tendorf, Jesus Astorga, Jonathan Perez, Jylian Hanson, Monica Delgadillo, Morgan Hannigan
TTU HCoA Course:
Spring 2024 | Arch 5354 TTU-Adv. Arch. Tech.
Urban Community Food Podium: Integrated Design to Robotic Production & AR-Enabled Assembly Systems
Authors of this Page: Caleb Scott
1:1 Prototypes and Full-Scale Material Exploration
The development of 1:1 prototypes and full-scale material assemblies marked a pivotal stage in translating digital design into tangible architecture. By shifting from scaled models and digital renderings to life-sized construction, students were able to engage with their projects in a way that revealed the complexities and realities of material behavior, structural logic, and spatial experience. This hands-on process required careful coordination, critical thinking, and iterative problem-solving, as teams worked to fabricate, test, and refine components using the actual materials intended for final installation.
Working at full scale allowed teams to understand the tolerances, weight, durability, and limitations of their materials—whether working with wood, masonry, metal, or hybrid systems. These tests informed joinery strategies, assembly sequences, and overall feasibility, helping to uncover issues that digital tools alone often obscure. In some cases, prototypes were deconstructed and reassembled multiple times to resolve structural challenges or optimize construction efficiency. In others, the act of physically building clarified the spatial qualities and user interactions that could only be sensed at full scale.
Beyond the technical benefits, the 1:1 prototyping phase encouraged a deeper respect for craft, labor, and the collaborative nature of building. It created a shared language between design teams, fabricators, and instructors, while also laying the groundwork for community involvement in the final construction. Ultimately, this phase bridged the gap between speculative design and built reality—reinforcing the value of full-scale prototyping as a critical and creative tool in the architectural process.
In addition, the process introduced students to the unpredictable realities of construction logistics and fabrication sequencing. They confronted challenges such as material warping, tool limitations, connection failures, and environmental exposure, all of which informed adaptations to both the design and the construction method. Many teams found that their digital models required revision once real-world constraints were introduced, emphasizing the importance of iterative workflows that move fluidly between the digital and the physical.
Full-scale testing also helped prepare for the integration of AR-enabled assembly, ensuring that the augmented reality guidance system would be both accurate and user-friendly. The clarity and feasibility of each joint or module depended on the tangible understanding gained through physical prototyping. Ultimately, these 1:1 explorations served as a rehearsal for the final construction, empowering students to move forward with greater confidence, technical understanding, and design intention.
Group 1 Landscape + Canopy
Brandon Paleo, Garrett Whitehead, Gunner Murrell, Jack Dittrich, Jacklyn Hurtado, Jakelin Silva, Kathleen Gutierrez, Max Halwas
Group 2 Oven + Canopy
Aaron Malavolta, Amanda Gomez, Apollo Nyoma, Caleb Scott, Gabe Herrera, Harmony Smith, Mattia Hajmeli, Robin Mutchler
Group 3 Landscape + Oven
Bahar Bagheri, Bernardo Lopez, Colin Ayers, Corinne Tendorf, Jesus Astorga, Jonathan Perez, Jylian Hanson, Monica Delgadillo, Morgan Hannigan