AI-Generated Design to Robotic 3D Printing
Caption here
AI-Infused Fusion: Orchestrating a Hybrid Wall with Seating
The Collaborative endeavor represents a pioneering group project focused on the creation of a hybrid wall structure seamlessly incorporating innovative seating elements, each defined by a distinctive pattern extruded outwardly. At the core of this design initiative is the strategic application of Artificial Intelligence (AI) to intricately guide and mold the formative aspects of the project. To establish a rich and varied design language, an assortment of images was meticulously sourced from the “MidJourney” platform. The selection process involved targeted prompts, encompassing thematic elements such as “steampunk,” “canopy,” “biomechanic,” “bench,” “wall,” and “organic,” thus serving as a foundation for the subsequent stages of the project.
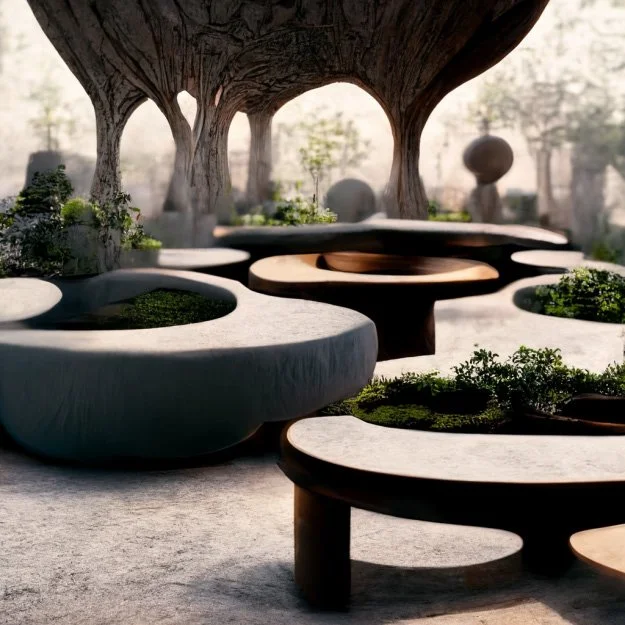



AI Precision: Unveiling the Power of Image Sampler in Design
The project’s creative trajectory is the integration of the Image Sampler, a sophisticated tool that was used with each image generated by the AI. This deliberate choice facilitates the extraction of data points meticulously aligned with the essential characteristics of the images. The application of the Image Sampler not only ensures a complex analysis but also opens avenues for the exploration of intricate and visually driven design possibilities. As a result, the project transcends conventional design methodologies, capitalizing on the symbiosis between AI-guided form generation and the systematic analysis of image attributes.

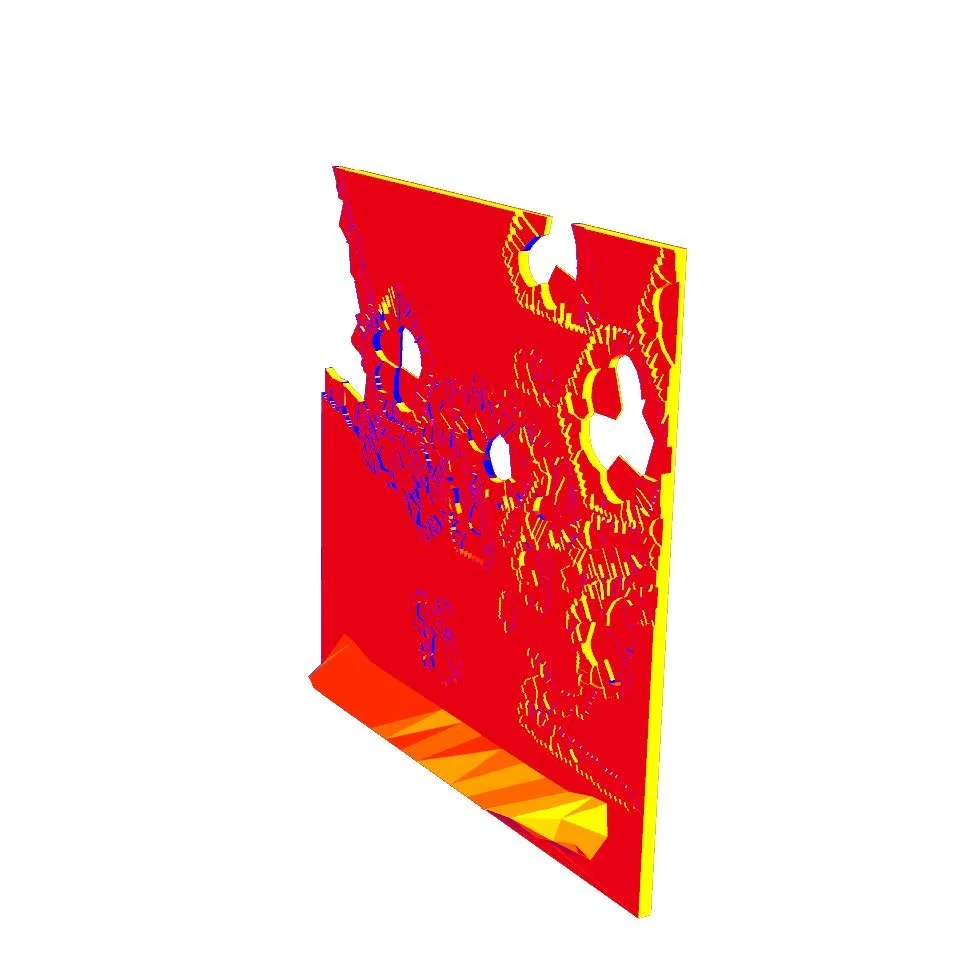



Hexagonal Harmony: Crafting a Robust Structure through Concrete 3D Printing
The culminating design iteration introduces a meticulously crafted hexagonal pattern, strategically incorporated to enhance the support within the seating area of the project. This final pattern served as a pivotal reference point for subsequent adjustments in density and quantity, yielding both negative and positive hexagonal geometries distributed across ten distinct levels. The translation of these diverse levels into a unified toolpath paved the way for the concrete 3D printing of a prototype. Noteworthy is the strategic execution of the toolpath, wherein the upper part of the geometry was initially printed, followed by the bottom portion. This sequential approach, mindful of the material deposition thickness, facilitated the creation of closed geometries with a single, precise toolpath attesting to the project’s commitment to both innovation and efficiency.
Credits
Texas Tech University Huckabee College of Architecture
Associate Professor: Dr. Sina Mostafavi
Graduate Research Assistants: Sarvin Eshaghi, Sepehr Vaez Afshar
Primary Participants: Abel Gonzalez, Edgar Montejano, Cristian Solis, Matthew Stevens, Benjamin Varner